ES&H Manual Chapter 45_45.7 Work Process J. Work Practice Controls
RETURN TO CH45 TABLE OF CONTENTS
Chapter 45
CHEMICAL HYGIENE AND SAFETY PLAN
____________________
Work Process J. Work Practice Controls
Work practice controls include pre-planning work, practicing good housekeeping, maintaining personal hygiene to minimize exposure to hazardous materials, and using common sense. Work practice controls must be used regardless of the type of hazardous material handled. This is not accomplished through the WPC process alone. This evaluation should be performed prior to the start of any task. The first three steps of the Integrated Safety Management (ISM) process should be employed prior to the initiation of work: Define the scope of your work; Identify all hazards associated with the work; Identify the controls necessary to mitigate those hazards.
- Work Planning
- Pre-plan work: Stage tools, equipment, and materials in advance of the activity to be performed.
- Establish designated areas for work involving particularly hazardous substances.
- Stay upwind or use exhaust ventilation for operations that emit vapors, gases, fumes, dusts, mists, or aerosols.
- Limit the amount of hazardous materials procured, used, and stored to the minimum needed for an operation.
- Keep drip pans, secondary containment and cleanup materials readily available.
- Be familiar with the use, limitations, and location of emergency equipment such as emergency eyewashes, safety showers, fire alarms, exits, and fire extinguishers.
- Keep containers covered when not being used.
- Remove jewelry to prevent contact with electrical sources and chemicals and from catching on laboratory or shop equipment.
- Confine long hair and loose clothing when working in the laboratory/shop.
- Housekeeping
- Keep work areas clean and free of obstructions. Clean the work area at the completion of an operation or at the end of the day.
- Wipe drips and residues from containers of hazardous materials. Skin contact with residues may cause dermal absorption, chemical burns, skin irritation, and possible accidental ingestion as a result of hand-to-mouth transfer.
- Clean surfaces (counter tops, bench tops, fume hoods, and floors) of all drips and residues.
- Clean spilled chemicals immediately, and dispose of all wastes properly. Spill response is discussed later. Chemical wastes must be disposed of in accordance with the ES&H Manual Waste Management program.
- Maintain access to exits, emergency equipment, and other control equipment. Do not use stairways and hallways as storage areas. Store equipment and chemicals properly, and avoid clutter.
- Personal Hygiene
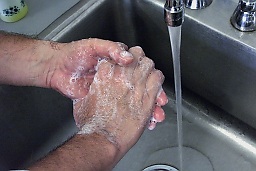
- After handling chemicals, wash hands with soap and water before leaving the laboratory/shop area and prior to breaks and consumption of food/beverages.
- Always remove gloves before touching common use items such as phones, doorknobs, and computers. This will prevent contamination of unprotected individuals.
- Food, Beverage, Cosmetics, and Medicine in Technical Areas
- Food and beverages (including water, gum, and medicines) may not be consumed or stored in technical areas. Exceptions may be granted in accordance with the procedure described in ES&H Manual Personal Protective Equipment (PPE) program, Appendix A, PPE and Food/Drink Requirements and Responsibilities Table.
- Cosmetics, ointments, skin cream, and similar items may not be applied or stored in technical areas.
- See Work Process K.1.b, Refrigerators and Freezers Used for Hazardous Material Storage, for requirements regarding food storage in refrigerators.
- Do not use laboratory glassware or utensils to prepare or consume food or beverages.
- Use of Glassware
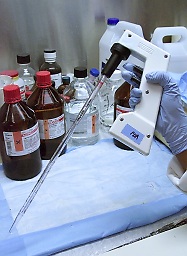
- Never use mouth suction to pipette chemicals or to start a siphon; use mechanical means, a pipette bulb, or an aspirator.
- Use adequate hand protection (e.g., proper gloves) when inserting glass tubing into rubber stoppers or corks or when placing rubber tubing on glass hose connections. Tubing should be fire-polished or rounded and lubricated, and hands should be held close together to limit movement of glass should fracture occur. Plastic or metal connectors should be used whenever possible.
- Do not attempt glassblowing operations unless proper annealing facilities are available.
- Handle vacuum-jacketed glass apparatus with extreme care to prevent implosions. Equipment such as dewar flasks should be taped or shielded. Only glassware designed for vacuum work should be used for that purpose. Consult the ES&H Manual Chapter 7, Pressure Safety and Cryogenics program, for the safe use of pressurized and evacuated systems.
- Protect hands (i.e., wear tear- and puncture-resistant gloves) when picking up broken glass.
- Disposal of Glassware. Dispose of glass in marked cardboard boxes designated for that purpose. Glassware must be free of liquids prior to disposal. Consult Section 2.2, Solid Medical/Biohazardous Waste Disposal, of the Medical and Biohazardous Waste Generator’s Guide (PUB-3095) for guidance on disposing of glassware that has been used for biological work or that may be contaminated with a biohazardous material.
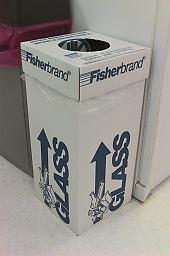
- Administrative Controls. Administrative controls include written procedures, employee training, establishing designated or restricted areas, chemical procurement procedures, and preventive maintenance. The development and use of written safety authorizations are discussed in the Work Planning and Control program (EH&S Manual Chapter 6). Training is discussed in Work Process W, Training, and Work Process X, Safety Data Sheets. The establishment and use of designated areas are discussed in Work Process M, Specific Controls and Procedures — Particularly Hazardous Substances: Carcinogens, Reproductive Toxins, and Acute Toxins.
____________________