ES&H Manual Chapter 45_45.7 Work Process P.1 Specific Controls and Procedures — Additional Time-Sensitive Chemicals
RETURN TO CH45 TABLE OF CONTENTS
Chapter 45
CHEMICAL HYGIENE AND SAFETY PLAN
____________________
Work Process P.1 Specific Controls and Procedures — Additional Time-Sensitive Chemicals
This work process outlines the requirements for the safe management of time-sensitive chemicals other than peroxide-forming chemicals. All owners of time-sensitive chemicals must follow the policy provided herein, including: tracking all containers of time-sensitive chemicals in the Chemical Management System; labeling all containers of time-sensitive chemicals; assessing all containers of time-sensitive chemicals on at least an annual basis; and working with EHS and Waste Management to safely manage and/or dispose of expired, unsafe or unneeded time-sensitive chemicals.
The work process is organized as follows:
• Section 1 gives a brief overview of what time-sensitive chemicals are and why they must be managed carefully.
• Section 2 identifies the key responsibilities for employees and affiliates at all levels who are involved with the use of time-sensitive chemicals.
• Section 3 lists the required training for those who work with time-sensitive chemicals.
• Section 4 describes how to properly track time-sensitive chemicals using the Chemical Management System.
• Sections 5 and 6 outline the requirements for engineering controls and personal protective equipment, respectively.
• Sections 7 through 10 provide the detailed policy for the labeling, assessment and handling of four categories of time-sensitive chemical: unstable/self-reactive with production of gaseous products; hazardous polymerization; explosive when dry; and time-sensitive gases.
• Section 11 details the process for getting rid of time-sensitive chemicals that are no longer needed, have passed their expiration dates, or are no longer safe to keep. Please note: do not place any time-sensitive chemicals into a satellite accumulation area (SAA) until they have been evaluated by your EHS Health and Safety Representative and the Waste Management Team.
• Section 12 contains some relevant Lessons Learned and incident reports involving time-sensitive chemicals.
- Time-Sensitive Chemicals
Time-sensitive chemicals can develop additional hazards during storage, even if stored and handled properly. Peroxide-forming organic chemicals are only one class of time-sensitive chemical, and this work process pertains to four other classes of time-sensitive chemicals.
It is important to recognize the potential hazards and the innate unpredictability of these chemicals. The rate at which a time-sensitive chemical becomes dangerous to handle depends on many factors. Even when stored properly, if ignored or forgotten a time-sensitive chemical can become unstable, unsafe or potentially explosive. When stored improperly or mishandled, time-sensitive chemicals can pose an immediate danger in the research environment.
The Environment, Health & Safety Division is available to provide assistance in identifying time-sensitive chemicals and determining the best storage conditions and other controls for storing and handling these materials. Contact your Health and Safety Representative or the Time-Sensitive Chemicals Subject Matter Expert (SME) for help.
- Requirements and Responsibilities
The chemical owner is ultimately responsible for the management of his or her time-sensitive chemical inventory. Responsibilities are assigned as follows:
Table 2.1 Responsibilities for the Management of Time-Sensitive Chemicals
Time-Sensitive Chemicals Subject Matter Expert | Maintain this policy with up-to-date and accurate information. Assist with the continual identification of time-sensitive chemicals. Remind chemical owners of the time-sensitive chemicals in their inventories and of the need to label, track and regularly assess containers of time-sensitive chemicals. Assist with the safe management of expired or unneeded time-sensitive chemicals, as necessary. |
Operations Staff | Evaluate stability of improperly managed time-sensitive chemicals; summary of roles and responsibilities for relevant Operations Staff can be found here. Note: these roles and responsibilities apply to Work Process P (management of peroxide-forming compounds) and Work Process P.1 (additional time-sensitive chemicals). |
Chemical Owner | Identify time-sensitive materials owned by you. Know the correct storage conditions and safe handling procedures for all time-sensitive chemicals that you are responsible for. Ensure that containers of time-sensitive materials are stored appropriately according to manufacturer’s instructions, SDS information, and/or other relevant sources. When time-sensitive materials are identified that are not categorized as such in the Chemical Management System, notify the CMS manager at cms@lbl.gov of the discrepancy. Ensure that all containers of time-sensitive materials are RFID tagged and entered into CMS. To the extent possible, ensure that all time-sensitive materials are tracked this way, including portions of time-sensitive materials transferred into secondary containers for storage. Affix an appropriate time-sensitive chemical label to all containers of time-sensitive materials. Assess the safety of all time-sensitive materials on a schedule commensurate with their hazard, as described in sections 7-10 of this document, and keep records of the results, in CMS (required) and either on the time-sensitive label or in an easily accessible log (strongly recommended). CMS tracking ensures test history will remain accessible regardless of personnel changes and that CMS testing notifications will be provided.  Note: the chemical owner may designate one or more Designated Responsible Person(s) to perform some or all of these duties. |
Designated Responsible Person(s) | Perform the duties of the chemical owner, as assigned, with the delegated authority of the chemical owner. |
Activity Lead | Identify time-sensitive materials used in the Activity. Maintain current description of work, hazards and controls in Activity Manager, and update the description of work whenever the scope of work changes. Provide, or designate a knowledgeable and authorized person to provide, on-the-job training to workers for all of the time-sensitive chemicals that the given worker will handle. Ensure that all workers know how to find the assessment records for time-sensitive chemicals. Determine the competency of workers to perform the work described by the Activity, and authorize workers in Activity Manager as appropriate. Notify the Chemical Owner or Designated Responsible Person of any label discrepancies, abnormal conditions, or lapses in the management of time-sensitive chemicals that are found. When time-sensitive materials are identified that are not categorized as such in the Chemical Management System, notify the CMS manager at cms@lbl.gov of the discrepancy. |
Worker | Identify time-sensitive materials used in the course of work. Receive appropriate on-the-job training for time-sensitive chemicals. Maintain current training in Chemical Hygiene and Safety (EHS 0348 and refresher course EHS 0353) and Managing Time-Sensitive Chemicals (EHS0394). Read and understand the Description of Work, Hazards and Controls information for all Activities. Follow safe practices for the use and storage of time-sensitive materials as laid out in the Activity, this work process, and as described and/or demonstrated in On-the-Job training. Know the location of assessment results for time-sensitive chemicals. Inform the Activity Lead and Supervisor of any abnormal conditions of time-sensitive material containers that are found. Notify the Chemical Owner or Designated Responsible Person of any label discrepancies, abnormal conditions, or lapses in the management of time-sensitive chemicals that are found. When time-sensitive materials are identified that are not categorized as such in the Chemical Management System, notify the CMS manager at cms@lbl.gov of the discrepancy. |
- Training and Additional Information
- Employees who manage, handle, or use time-sensitive chemicals must complete EHS 0348, Chemical Hygiene and Safety Training (or EHS 0345 for Facilities personnel), and complete the Chemical Hygiene and Safety Training Refresher course, EHS 0353, every three years thereafter, and Managing Time-Sensitive Chemicals (EHS0394).
- Employees who handle time-sensitive chemicals must also read and be familiar with this Work Process and receive on-the-job training (OJT) in the hazards, controls and storage requirements for the specific materials being handled.
- Information on the identification of time-sensitive chemicals may be found in Sections 7-10 for each category of time-sensitive material.
- For information regarding the management of time-sensitive chemicals in general, see Management of Time-Sensitive Chemicals, parts (I) through (III), in the Journal of Chemical Health and Safety authored by Jim Bailey et al (parts I and II) and David Quigley et al (part III)1.
- Employees who handle time-sensitive chemicals are also highly encouraged to consult Bretherick’s Handbook of Reactive Chemical Hazards Sixth or Seventh Edition, Volume 2, and the associated references in Volume 1 of the same and in the literature. A copy of both volumes is available for your reference with the Time-Sensitive Chemical Subject Matter Expert.
- More specific references for each category of time-sensitive chemical are provided where relevant throughout the work process.
1 Bailey et. al. Management of time sensitive chemicals (I): Misconceptions leading to incidents. Chem. Health Safe. 2004, 11(5), 14-17.
Bailey et. al. Management of time sensitive chemicals (II): Their identification, chemistry and management. Chem. Health Safe. 2004, 11(6), 17-24.
Quigley et. al. Management of time sensitive chemicals (III): Stabilization and treatment. J. Chem. Health Saf. 2006, 13(1), 24-29.
- Chemical Inventory Management
- All time-sensitive chemicals must be entered into the Chemical Management System (CMS) for chemical inventory tracking. The chemical owner or designated responsible person shall ensure that all containers of time-sensitive chemicals, whether in the manufacturer’s container or having been transferred in whole or in part to a new container, are entered into CMS with all relevant information including the date of acquisition of the original container.
- Exceptions
- Containers that are in use and will be emptied or disposed at the end of the experiment or procedure.
- Also see Section 8 for quantity exceptions for chemicals that undergo hazardous polymerization.
- Best Practices
- Before purchasing a time-sensitive chemical, it may be beneficial to use a small amount from another research group to test the procedure and ensure that the chemical will meet the research needs.
- Time-sensitive chemicals should be purchased in the smallest practical quantities to avoid accumulation of leftover or unneeded material.
- Periodic chemical inventory clean-outs can help reduce accumulation of time-sensitive chemicals. A recommended time period is every 2-3 years.
Note: LBNL policy for chemical inventory tracking does not generally require materials transferred out of the original manufacturer’s container to be
RFID tagged
and entered in the Chemical Management System. However, due to the inherent dangers of time-sensitive chemicals, every container (including bottles, jars, vials, etc.) must be
RFID tagged
and tracked
in CMS
if it is to be stored.
- Engineering Controls. Engineering controls for the use of time-sensitive chemicals shall be selected based on the hazards of the particular substance(s).
- See Work Process H for general information on engineering controls. EHS is available to assist with selection of proper engineering controls.
- The following work processes may be consulted for more information on controls for handling chemicals with specific hazards:
• Work Process L, Acids and Bases
• Work Process M, Particularly Hazardous Substances: Carcinogens, Reproductive Toxins, and Acute Toxins
• Work Process N, Flammables and Combustible Liquids
• Work Process Q, Water-Reactive Chemicals
• Work Process R, Pyrophoric Materials
• Work Process T, Chemicals with Explosive Properties
- Personal Protective Equipment
- Minimum personal protective equipment when working with time-sensitive chemicals consists of:
• Long pants
• Closed toe shoes
• Safety glasses with side shields
• A laboratory coat
• Chemically resistant gloves
- Consult the Safety Data Sheet of the particular chemical and/or manufacturer glove compatibility literature, for the appropriate glove type(s).
- See Work Process I, Personal Protective Equipment for more information on selection of appropriate PPE, including the use of cover goggles, face shields, aprons and chemically resistant sleeves. EHS is also available to assist with proper PPE selection.
- Unstable/Self-Reactive with Production of Gaseous Products
- Description of Hazard. Some chemicals self-react or decompose to generate heat and gaseous products 2 . In some cases, the products of the self-reaction also accelerate the reaction 3 . Even if these chemicals do not undergo thermal runaway due to the generation of heat, the constant buildup of gas inside the container can lead to eventual over-pressurization and violent container rupture. The introduction of moisture into chemicals of this type will often initiate or accelerate the decomposition or self-reaction.
- Identification. Specific chemicals and chemical categories that are known to self-react to produce gaseous products are listed, with examples, in the table below. Many of these undergo autocatalytic decomposition or condensation reactions.
Table 7.1 Specific Chemicals with Pressure Hazards During Storage
Specific Chemicals | CAS | Synonyms |
Formic acid (≥ 98%) | 64-18-6 | Methanoic acid |
Hydrogen Peroxide (≥ 30%) | 7722-84-1 | Dioxidane; Oxidanyl; Perhydroxic acid |
Hydroxylamine | 7803-49-8 | Azinous acid; Aminol; Azanol; Hydroxyamine; Hydroxyazane; Hydroxylazane; Nitrinous acid |
Borane-Tetrahydrofuran | 14044-65-6 | Borane-THF complex; Tetrahydrofuran compd. with borane |
Table 7.2 Chemical Categories with Pressure Hazards During Storage
Chemical Categories | Examples |
Chloroformates | Benzyl chloroformate (used for cbz protection); ethyl chloroformate; n-butyl chloroformate; sec-butyl chloroformate; isobutyl chloroformate; propargyl chloroformate; Fmoc chloride; nitrobenzyl chloroformate; nitrophenyl chloroformate; trichloroethyl chloroformate |
Benzyl halides2 | Benzyl fluoride; Benzyl chloride; Benzyl bromide; Methylbenzyl chloride; Methylbenzyl bromide; Vinylbenzyl chloride; Methoxybenzyl chloride; Chloroxylene; α,α’-Dibromo-p-xylene; Methyl α-bromophenyl acetate |
Halomethyl furans2 | 2-Chloromethylfuran; 2-Bromomethyl-5-methylfuran |
Furoyl halides (Furan carbonyl halides) | 2-Furoyl chloride; 3-Methylfuran-2-carbonyl chloride |
Halomethyl thiophenes2 | 2-Chloro-5-(chloromethyl)thiophene |
Thiophene carbonyl halides | 2-Thiophenecarbonyl chloride |
Benzene sulfinyl/sulfonyl halides | Benzene sulfinyl chloride; Benzene sulfonyl chloride |
2 Gas Evolution Incidents. Bretherick’s Handbook of Reactive Chemical Hazards, 6th Edition, pp 147-148.
3 Benzyl Compounds. Bretherick’s Handbook of Reactive Chemical Hazards, 6th Edition, pp 54-55.
2-Halomethyl-Furans or -Thiophenes. Bretherick’s Handbook of Reactive Chemical Hazards, 6th Edition, pp 167-168.
- Storage
- Many chemicals in this category are stored cold to slow the self-reaction or decomposition. However, not every manufacturer’s SDS contains complete storage information. It is recommended that owners of this category of time-sensitive chemical check multiple SDS documents and any other available sources to ensure complete information on the storage requirements.
- Most of the chemicals in this category are also sensitive to contamination, which will increase the rate at which they react or decompose to produce gas.
- Many are water-reactive (especially the chloroformates, furoyl halides and thiophene carbonyl halides) and even a small amount of moisture may cause a rapid buildup of pressure in the container.
- Labeling, Assessment and Venting
- All containers of this class of time-sensitive chemical shall bear a label identifying them as a time-sensitive chemical. Additionally, the Designated Responsible Person must keep
CMS testing records up to date
that contain:
- Date the container was opened
- Inspection frequency
- Date and result of all inspections
Note: It is strongly recommended to also keep testing records either on the label or in an easily accessible log.
- Once opened, this classification of time-sensitive chemicals shall be assessed on a schedule commensurate with its hazard as communicated by the manufacturer, in the SDS, in the relevant literature, and/or in the experience of the research group.
- The assessment period in any case shall not be greater than one year. In many cases, the assessment period for chemicals of this type should be significantly less than one year. For help determining an appropriate assessment period, contact the Time-Sensitive Chemical subject matter expert.
- During each assessment, the container shall be carefully vented. Note that the presence of a vented cap on the container does not exempt the container from this requirement.
- A lab coat and appropriate chemical resistant gloves must be worn while venting containers.
- This procedure shall be performed in a fume hood or glove box if appropriate.
- The bottle is opened slowly and carefully to allow excess pressure to escape, then re-closed.
- Venting of air- or water-sensitive chemicals supplied with a septum cap may be accomplished using needles. A low pressure inert gas supply may be used to prevent backflow of air into the container.
- The safety of a container in this classification shall be assessed visually by checking for the following failure criteria:
- Prolonged abnormal storage conditions such as storage at room temperature when the SDS or manufacturer’s instructions indicate cold storage;
- Any evidence of pressure build-up in the container, such as a bulging cap;
- The container has passed the expiration date provided by the manufacturer.
- Any time-sensitive material container that fails any one of these criteria shall be considered unsafe or expired, and the procedure in Section 11 shall be followed for the safe management and disposal of the container.
Note: If the container has yet to be opened, do not open it to vent or assess it. The periodic assessment cycle commences when the container is first opened.
- Handling Considerations
- Vent previously opened containers frequently, especially if they are rarely used.
- Heating this class of chemicals may increase the decomposition rate drastically or lead to a thermal runaway. Carefully consider all reaction conditions before heating this class of chemical, including conditions for safely venting any gaseous products that may result.
- Store containers with vented caps in a fully upright position to prevent leaks. The presence of a vented cap does not exempt the container from regular assessment and venting of previously opened containers.
- Ensure that all tools used, such as spatulas or pipettes, are clean and dry. This class of chemical is particularly sensitive to contamination, which includes moisture in many cases.
- Never return unused portions of the chemical to the original container.
- Do not mix the chemical with any incompatible materials when disposing of unused chemical portions or mixtures containing unused chemicals in this category. This may lead to pressure buildup in the waste container. It may be safest to use a dedicated container with no other materials.
- Metal containers and caps can be a source of contamination, and some of the materials in this class are initiated or catalyzed by metals and/or metal oxides such as iron or rust.
- Hazardous Polymerization
- Description of Hazard. Many monomers are supplied with an inhibitor added to prevent polymerization until the experimenter intentionally initiates it. This leads to greatly prolonged shelf lives of monomers that may otherwise polymerize, sometimes violently, in a short period of time. However, the inhibitors used are often sacrificial by nature, and thus during prolonged storage and exposure to adverse conditions the inhibitor concentration may decrease over time. Eventually the inhibitor concentration may decrease to the point that it is no longer effective and polymerization will begin. Not only does this lead to a useless reactant, but the reaction is usually exothermic and accelerates with increasing temperature, which can produce considerable heat and rupture containers with significant force4. This process is known as thermal runaway. The potential for violent polymerization largely depends on the nature of the chemical, but for any one substance the risk is increased with increasing container size. Industrial accidents involving runaway polymerizations of stored material are frequent and sometimes deadly to those involved 5. Accidents of this nature rarely happen on the laboratory scale because small containers are capable of releasing heat to the environment faster than their internal volume can produce heat by reaction. Often, small bottles will simply polymerize over time with no detrimental effects. However, on a larger scale the risks are well documented, including fires and explosions resulting in severe injury and loss of life. Therefore, any production-scale containers of materials that can undergo hazardous polymerization upon consumption of the inhibitor must be carefully tracked and managed to prevent accidents.
- Identification
- Small volumes of the chemicals in this category pose very little risk of accident. Therefore, only production-scale quantities of this category are considered time-sensitive for the purposes of this policy. Researchers should consider the special considerations (reactivity, exothermic properties, quantity) of the chemicals that they are using and determine if and how the chemicals should be managed. EHS can assist with this determination. Research-scale quantities of monomers with a hazardous polymerization hazard may be handled, stored and tracked in the same manner as chemicals that are not time-sensitive.
- There is some overlap between chemicals that undergo hazardous polymerization and peroxide forming organic chemicals. Both the formation of organic peroxides and the initiation of hazardous polymerization start with the homolytic cleavage of a weak C-H bond to form a radical. In the presence of oxygen, this radical may combine with dissolved oxygen to produce an organic peroxide. In the absence of oxygen, the radical may initiate polymerization. For more information, see Work Process P: Specific Controls and Procedures – Organic Peroxide-Forming Compounds. A list of chemicals that are known or suspected to have undergone violent polymerization can be found here. It is not exhaustive.
- Some of the most common chemical categories that undergo hazardous polymerization are included in the table below.
4 Polymerization Incidents. Bretherick’s Handbook of Reactive Chemical Hazards, 6th Edition, Volume 2, pages 324-327.
Violent Polymerization. Bretherick’s Handbook of Reactive Chemical Hazards, 6th Edition, Volume 2, pages 397-398
5 Calorimetric evaluation of polymerization thermokinetics of styrene, -methylstyrene and trans-methylstyrene. S.Y. Lin, K.Y. Chen, C.M. Shu, Journal of Hazardous Materials 161 (2009) 330-335.
Table 8.1 Chemical Categories Prone to Hazardous Polymerization at Production Scale
Category | Common Examples |
Acrylates | Acrylic acid, Methacrylic acid, Methyl methacrylate, Butyl methacrylate |
Epoxides and Ethylene imines (aziridines) | Ethylene oxide, Propylene oxide, Diepoxybutane, Epichlorohydrin, 2-Methylaziridine, 11-Azatricyclo[4.4.1.0(1,6)]undeca-3,8-diene |
Short Chain Conjugated Dienes | 1,3-Butadiene, Isoprene |
Styrenes | Styrene, 2-bromostyrene, 4-benzhydrylstyrene, α-chlorostyrene |
Vinyl monomers | Vinylcyclohexene, vinyl acetate, 4-vinylpyridine, Methyl vinyl ketone |
- The most commonly used chemicals at LBNL that undergo violent polymerization in production-scale quantities are shown in the table below.
Table 8.2 Commonly Used Chemicals at LBNL Known to Polymerize Violently at Production Scale
Chemical Name | CAS Registry Number | Synonyms |
Acrylaldehyde | 107-02-8 | Acrolein; Acrylic aldehyde; Allyl aldehyde; Prop-2-enal |
Acrylamide | 79-06-1 | Acrylic amide; Prop-2-enamide |
Acrylic acid | 79-10-7 | Acroleic acid; Ethylenecarboxylic acid; Propenoic acid; Vinylformic acid |
1,3-Butadiene | 106-99-0 | Butadiene; Biethylene; Divinyl; Vinylethylene |
Furfuryl alcohol | 98-00-0 | 2-Furylmethanol; 2-Furancarbinol |
p-Coumaric acid | 7400-08-0 | 4-Hydroxy-trans-cinnamic acid; p-Cumaric acid; 4-Hydroxycinnamic acid
|
- Storage. The manufacturer’s instructions (if provided) and the SDS must always be followed where they conflict with or are more specific than the general guidance offered here.
- Storage Temperature: This class of time-sensitive chemicals is generally stored cold but not frozen.
- Storage Containers: Many of this class of material are light-sensitive, requiring storage in either opaque containers or amber glass bottles.
- Other Considerations – Atmosphere: The gas occupying the headspace of a container can modify the behavior of chemicals in this category. In the absence of dissolved oxygen, the conversion of carbon radicals to peroxides is not possible, and the formation of radicals is more likely to result in the initiation of hazardous polymerization 6. However, with the presence of dissolved oxygen, these chemicals may accumulate organic peroxides and may need to be managed according to Work Process P: Specific Controls and Procedures – Organic Peroxide-Forming Compounds.
6 Acrylic Monomers. Bretherick’s Handbook of Reactive Chemical Hazards, 6th Edition, Volume 2, page 5.
- Assessment and Labeling
- Production-scale quantities of this classification of time-sensitive chemical shall be assessed on a schedule commensurate with their hazard as communicated by the manufacturer, in the SDS, and/or in the relevant literature.
- The assessment period in any case shall not be greater than one year.
- The safety of a container in this classification shall be assessed visually by checking for the following failure criteria:
- Prolonged abnormal storage conditions such as storage at room temperature when the SDS or manufacturer’s instructions indicate cold storage;
- Any evidence of pressure build-up in the container, such as a bulging cap;
- Any evidence of polymerization, such as solid residue in the container;
- The container has passed its expiration date as provided by the manufacturer.
- Any time-sensitive material container that fails any one of these criteria shall be considered unsafe or expired, and the procedure in Section 11 shall be followed for the safe management and disposal of the container.
- All containers of this class of time-sensitive chemical shall bear a label identifying them as a time-sensitive chemical. Additionally, the Designated Responsible Person must keep
CMS records up to date that
contain:
- Date the container was opened
- Inspection frequency
- Date and result of all inspections
Note: It is strongly recommended to also keep testing records either on the label or in an easily accessible log.
- Handling Considerations
- Heating this class of chemicals may lead to violent polymerization and thermal runaway, which may release toxic vapors, over pressurize and rupture containers, or ignite fires.
- Avoid freezing of liquids, as the frozen domains will exclude the inhibitor and the process of thawing the material may initiate polymerization. As the material thaws, local areas of uninhibited material can initiate a violent reaction, even under mild/ambient heating or thawing conditions. Uneven heating can also cause localized hot spots within the material that can initiate a thermal runaway polymerization.
- Metal containers and caps can be a source of contamination, and some of the materials in this class are initiated or catalyzed by metals and/or metal oxides such as iron or rust.
- Store in a cool, dry, dark place to avoid temperature fluctuations and exposure to light.
- Exercise great care when initiating large-scale polymerization reactions. Long induction periods can lead to an underestimation of the reaction progress and eventual reaction rate. This has caused many industrial accidents. 7
7 Induction Period Incidents. Bretherick’s Handbook of Reactive Chemical Hazards, 6th Edition, Volume 2, pages 183-184.
- Explosive When Dry
- Description of Hazard. This category encompasses substances that are shock-, friction- or heat-sensitive explosives when dry, but which have been stabilized with liquid for safer handling and transportation. If the substance is purchased and/or stored dry, then it falls under the controls in Work Process T, Chemicals with Explosive Properties. While sufficiently wetted or in solution, these materials can be handled without risk of detonation. However, if the liquid or solvent evaporates upon prolonged storage, the sensitive explosive material will be left behind and there is a risk of inadvertent detonation. The liquid used is sometimes quite volatile, such as diethyl ether or ethanol, and can evaporate quickly if containers are not properly resealed. Most reported incidents involving this class of material involve the friction-initiated detonation of dry crystals, either during scraping of the material as with a spatula, or when material has dried in the threads of the cap and the bottle is then opened.
In addition to the risks associated with the material drying out, many of these chemicals also form incredibly sensitive explosives on contact with metals, whether wetted or not. For example, picric acid is only moderately shock sensitive, but metal picrates are incredibly sensitive to shock, friction, heat and electrostatic discharge, making them extremely dangerous to handle even when wetted. It is important to check the SDS thoroughly for incompatibilities and to avoid contaminating the material with anything that might increase its explosive sensitivity.
- Identification. The most well-known explosives are polynitro organic compounds and nitrate esters such as nitroglycerin, trinitrotoluene (TNT), nitrocellulose (also known as collodion when wetted) and picric acid (trinitrophenol). However, many other functional groups can confer explosive properties and sensitivity to shock, friction or heat.
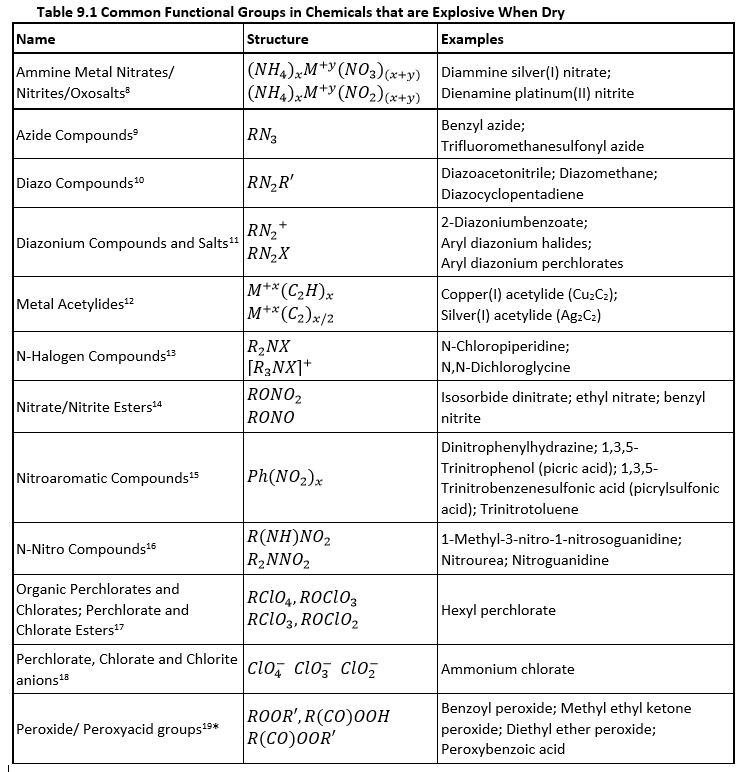
*Hydroperoxides, of the formula ROOH, can inadvertently be converted to mixed peroxides or react violently in the presence of trace metals. Concentration can then lead to violent explosion. See The Journal of Organic Chemistry, 1997, 62 (12), pp 3849–3857 and Chemical & Engineering News (31 May 1993) Vol. 71, No. 22, pp. 4.
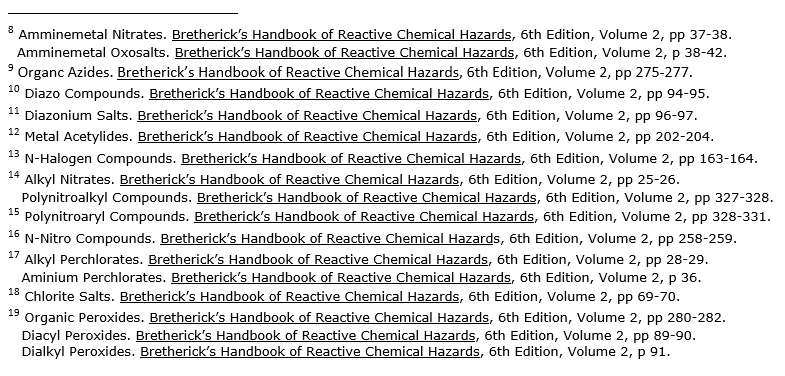
- Explosive When Dry Chemicals with Special Handling and/or Additional Controls
- Some specific compounds and categories of compounds are:
- known to be particularly sensitive to shock, friction or heat when dry;
- known to have caused multiple incidents in the laboratory setting; or
- potentially explosive even when wetted.
- These materials must be handled with extreme care and will require more extensive planning and review prior to acquisition. Researchers who wish to order and use these compounds or any chemical in one of these categories should work with their division Health and Safety Representative, Division Safety Coordinator, and Environmental Health and Safety Subject Matter Expert to plan specific controls and safeguards.
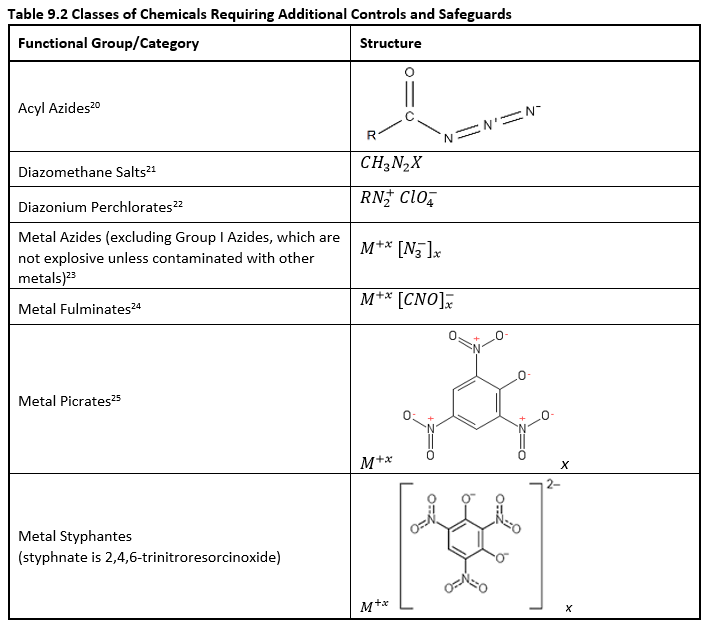
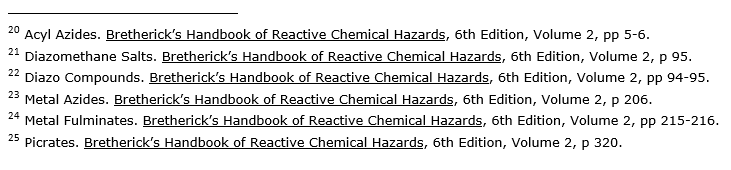
Table 9.3 Specific Chemicals Requiring EHS Consultation and Approval
Chemical Name | CAS Registry Number | Synonyms |
Picric Acid | 88-89-1 | 2,4,6-trinitrophenol |
Picrylsulfonic Acid | 2508-19-2 | 2,4,6-trinitrobenzenesulfonic acid |
These chemicals appear on the Restricted Items List and require approval for purchase.
- All primary explosives are prohibited at Lawrence Berkeley National Laboratory, whether wetted or not. Primary explosives are incredibly sensitive to heat, shock, friction or electrostatic discharge. These materials are often used to initiate other, less sensitive explosives. Common primary explosives include: acetone peroxide (triacetone triperoxide), diazodinitrophenol (DDNP), hydrazinium perchlorate, hydroxylammonium nitrate, lead azide, lead picrate, ammonium chlorate, silver fulminate, mercury fulminate, nitroglycerin, and pentaerythritol tetranitrate (PETN). Additional primary explosives may be found on the LBNL Restricted Chemicals and Gases List found here. This list is not exhaustive. It is the responsibility of the researchers to determine whether a material is a primary explosive using resources such as SDS documents, literature reports, and manufacturer-provided information. EHS can assist with identification. See Work Process T, Chemicals with Explosive Properties for more information.
- Storage
- Materials that are explosive when dry shall be stored in tightly closed containers in cool, dark locations to minimize evaporation.
- If the liquid or solvent is a flammable or combustible liquid, these materials must be stored in an approved flammable storage cabinet with self-closing, self-latching doors.
- It is recommended that these materials be stored inside a sturdy cabinet away from other materials where they are unlikely to be disturbed when not in use.
- Assessment and Labeling
- The safety of chemicals in this classification shall be assessed by visual inspection for the following failure criteria:
- There is evidence of significant evaporation as indicated by a liquid level marking. For modest evaporation, top up to level marking with appropriate solvent to stabilize material until the next assessment date;
- Solid material has precipitated from solution (in cases where the material is soluble in its stabilizing liquid);
- Crystals or solid material are visible around the bottom of the cap;
- Crystals or solid residue has formed on the outside of the container from dripping or leaking of the contents.
- Any time-sensitive material container that fails any one of these criteria shall be considered unsafe or expired, and the procedure in Section 11 shall be followed for the safe management and disposal of the container.
- Determining an appropriate assessment period for this class of time-sensitive chemical is crucial.
- In some cases, an Explosive When Dry material may be supplied with just enough liquid to stabilize the material. For example, picric acid/picrylsulfonic acid is often supplied in a near-concentrated solution, so any evaporation may lead to crystallization of the explosive material. These materials should have a shorter assessment period, such as one to three months.
- In other cases, an Explosive When Dry material may be supplied with a large excess of solvent, and need only stay wetted or moist to remain stable. For example, nitrocellulose, also known as collodion, is often supplied under a large excess of solvent. The assessment period for these materials can therefore be longer, but may not exceed one year.
- Some factors to consider when determining an appropriate inspection period include:
- Volatility/evaporation rate of the solvent or liquid that stabilizes the material;
- Concentration of the material in the solvent/liquid;
- Whether the material is stabilized by the mere presence of some wetting liquid, or must remain below a critical concentration for stability.
- In any case, the inspection period shall not be greater than 12 months.
- Each container of this class of time-sensitive chemical shall bear a label identifying it as a time-sensitive chemical. Additionally, the Designated Responsible Person must keep
CMS testing records up to date
that contain:
- Date the container was opened
- Inspection frequency
- Date and result of all inspections
Note 1: If a particularly sensitive explosive, such as diazomethane, is produced in the laboratory in a stabilizing solution or liquid, it shall not be stored for later use. It must be used in its entirety or quenched at the end of the process.
Note 2: It is strongly recommended to also keep testing records either on the label or in an easily accessible log.
- Handling Considerations
- Check the SDS carefully for incompatibilities that might increase the explosive sensitivity of explosive when dry materials. In particular, some of these materials are incompatible with metals, and care must to be taken to avoid the use of metal containers, lids, linings and tools.
- Never scrape explosive when dry material, even when still wetted. Multiple explosions have occurred during recovery of an explosive when dry material from the filter of a Büchner funnel due to scraping.
- Mark the liquid level on the outside of the bottle of containers of explosive when dry materials to track evaporation so that the liquid can be topped off as necessary. Always use a liquid or mixture with identical composition to the liquid/solvent provided by the manufacturer.
- Wrapping the cap with a gas-impermeable tape, such as electrical tape, may slow the evaporation rate. Note that Parafilm® is manufactured to be permeable to gases and may not significantly slow evaporation.
- Heating an explosive when dry material may cause solvent loss and/or detonation of the material
- Use only tools that are compatible with the material. Some materials are sensitive to contamination with metals and should not be handled with metal tools. Others may be sensitive to static discharge and should not be handled with disposable plastic tools. Teflon coated tools offer the best resistance to both metal contamination and static discharge. However, the teflon coating can become scratched or damaged, revealing the metal beneath. Check tools carefully for compatibility and for defects before use with explosive when dry materials.
- Metal containers, caps and trays can also be a source of contamination. Use plastic caps whenever possible, and avoid storing these containers in metal trays.
- Avoid the use of glass stoppers or ground glass joints. The friction/scraping of ground glass joints can initiate explosions if material dries between the two glass pieces.
- Time-Sensitive Gases
- Description of Hazard. This class of time-sensitive chemicals refers to pure gases or mixtures of gases that, due to their high reactivity, have the potential to over-pressurize, rupture, or corrode the cylinder in which they are provided. The valves on the cylinder may become corroded and blocked, causing the regulator to read zero pressure while there is still significant gas in the cylinder. If corrosion of valves or regulators is likely, a scale can be placed under the cylinder to keep track of its weight, rather than relying on the regulator pressure reading to determine how much gas is left in the cylinder.
In addition to the physical hazard of a cylinder failure, these gases are also highly toxic and/or reactive and present a major threat to life and health if they are released. In some cases, it may not be possible for someone entering the area after such an event to determine by sight or smell that the area is dangerous to enter. Further, gases have the potential to be released far outside the boundaries of a single room in which they are stored.
- Mixtures that include a low concentration (≤ 5%) of one of these gases in inert gas are not considered time-sensitive. Mixtures with more than 5% of one of these gases shall be assessed on a case by case basis using the professional judgement of the chemical owner and/or Designated Responsible Person, with consultation from EHS.
- It is especially important with these gases to be aware of all requirements and handling procedures for compressed toxic gas cylinders, as described in the ES&H Manual, Chapter 13, Gas Safety.
- Identification
- Gases that are known or reasonably suspected to have the capability to corrode or rupture their own cylinders upon prolonged storage are listed below.
Table 10.1 Time-Sensitive Gases
Name | CAS Registry Number | Default Shelf Life (if none provided by manufacturer) |
Hydrogen Bromide | 10035-10-6 | 5 years |
Hydrogen Cyanide | 74-90-8 | 90 days |
Hydrogen Fluoride | 7664-39-3 | 1 year |
Hydrogen Iodide | 10034-85-2 | 5 years |
- Return cylinders to the distributor or initiate the disposal process before the end of the cylinder’s shelf life.
- Storage
- Location: In general, containers of gases that are capable of rupturing their own cylinders are stored in an approved gas cabinet due to their toxicity and/or other hazards. Where not required to be stored in an approved gas cabinet, cylinders shall be seismically restrained and stored in accordance with ES&H Manual Chapter 13, Gas Safety.
- Condition: Store cylinders of these materials in a cool, dry location whenever possible. If cylinders are stored outside or in a wet or humid environment, ensure that all parts are fully dry before connecting a regulator and opening the cylinder. Water contamination can greatly increase corrosion rates.
- Assessment and Labeling
- This classification of time-sensitive chemical shall be monitored at least once every 6 months for the following failure criteria:
- Signs of corrosion or damage to the cylinder, especially near welding or valves, including frozen or stuck valves or blockages in the valve or regulator;
- Increased pressure inside the cylinder as read by a regulator (Note: if the cylinder is not connected to a regulator, do not connect it and open it simply to check);
- The expiration date/date of return as provided by the manufacturer has been met or exceeded or the cylinder has passed its default shelf life (see table above) and an expiration date or date of return was not provided by the manufacturer.
- Any time-sensitive material container that fails any one of these criteria shall be considered unsafe or expired, and the procedure in Section 11 shall be followed for the safe management and disposal of the container.
- If a corroded and blocked connection is suspected, close the valve on the cylinder and contact your Division Safety Coordinator and the Gases (Compressed/Hazardous/Toxic) subject matter expert for assistance.
- All containers of this class of time-sensitive chemical shall bear a
label or hang-tag
identifying them as a time-sensitive chemical.
CMS and
the label or tag must include the following information:
- A warning of potential for the gas to rupture its cylinder
- Date the cylinder was received
- Date the cylinder must be returned or disposal initiated
- Management and Disposal of Unsafe, Expired or Unneeded Containers
- When any time-sensitive chemical, as covered by this policy, fails its assessment criteria (see Sections 7-10), exceeds its expiration date, or is no longer needed, the following steps shall be taken to ensure safe and compliant management of the container:
- If there is any reason to believe that the container poses an immediate danger, evacuate the immediate area and notify your Health and Safety Representative of the situation.
- If the container does not pose an immediate danger, contact your Health and Safety Representative and Waste Services Team Generator Assistant for evaluation of the container before taking any other actions. Do not store any time-sensitive materials in an SAA, WAA or MWSAA prior to evaluation by your Health and Safety Representative and Waste Services Team.
- Under the supervision of your Health and Safety Representative, remove any incompatible materials from the area of the time-sensitive chemical, if needed.
- Once your Health and Safety Representative and Generator Assistant have determined that the container is safe to handle, the Waste Services Team will determine the most appropriate plan for disposal.
- If it is determined that the container is not safe to handle, an independent contractor will be called in to develop a plan and remove the unsafe container from site.
- Only once instructed by the Waste Services Team to do so, follow the Waste Management Generator Guidelines, PUB-3092, for safe and compliant disposal of the container.
- Lessons Learned
- Unstable/Reactive with Production of Gaseous Products
- Rust destabilized 4-nitrophenyl chloroformate:
http://www.crhf.org.uk/incident48.html
- In 1943, pressure buildup in a bottle of stabilized ethyl chloroformate showered a stockroom worker at Cal Tech with a significant quantity of the chemical. The stockroom worker died at the hospital that night.
http://cenblog.org/the-safety-zone/2012/04/historical-accidents-at-caltech-via-linus-paulings-notebooks/
http://scarc.library.oregonstate.edu/coll/pauling/rnb/16/16-045.html
- Hazardous Polymerization
- Thermal runaway of acrylic acid caused large release of liquid and vapor and subsequent fire:
http://www.crhf.org.uk/incident88.html
- Explosive When Dry
- A diazonium chloride salt precipitated from a supersaturated solution and detonated, killing the operator and injuring another:
http://www.crhf.org.uk/incident71.html
- A postdoctoral researcher was injured while scraping residue of an explosive material from a filter paper. The explosive compound had been wetted during the procedure, but the residue had dried sufficiently that the scraping cased a detonation:
https://ehs.berkeley.edu/lesson-learned-dry-scraping-causes-chemical-explosion
- While not directly caused by an explosive when dry compound, an incident involving sodium azide illustrates the severe consequences of contamination leading to more sensitive explosives. A low concentration sodium azide solution had been added to a particular piece of equipment to prevent algal growth in the water reservoir. A researcher removed a brass filter from the unit to clean it, and an explosion occurred during the cleaning procedure. While sodium azide is not sensitive to shock or friction, the copper azide formed on contact with the brass filter is a shock and friction sensitive explosive.
http://www2.lbl.gov/ehs/Lessons/pdf/LL_azidesv1.pdf
- Time-Sensitive Gases
- An old lecture bottle of anhydrous hydrogen fluoride became over-pressurized and ruptured, causing extensive damage to a laboratory.
https://lessonslearned.lbl.gov/Open/preview.aspx?id=144
- Liquid hydrogen cyanide cylinders are known to undergo polymerization upon depletion of the added acid stabilizer. If heated, or if polymerized material from the wall of the cylinder falls into the liquid, the polymerization may proceed at an accelerating rate, causing a large explosion with release of unreacted HCN and other toxic gases.
http://osha.oregon.gov/OSHARules/interps/im-94-20.pdf
____________________